An ACHE is a device for rejecting heat from a fluid directly to ambient air.
The obvious advantage of an ACHE is that it does not require water, which means that plants requiring large cooling capacities need not be located near a supply of cooling water.
An ACHE consists of the following components:
- One or more bundles of heat transfer surface.
- An air-moving device, such as a fan, blower, or stack.
- Unless it is natural draft, a driver and power transmission to mechanically rotate the fan or blower.
- A plenum between the bundle or bundles and the air-moving device.
- A support structure high enough to allow air to enter beneath the ACHE at a reasonable rate.
- Optional header and fan maintenance walkways with ladders to grade.
- Optional louvers for process outlet temperature control.
- Optional recirculation ducts and chambers for protection against freezing or solidification of high pour point fluids in cold weather.
- Optional variable pitch fan hub for temperature control and power savings.
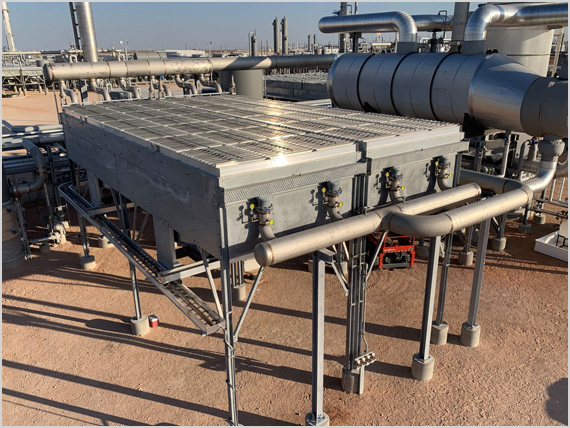

Induced Draft Configuration
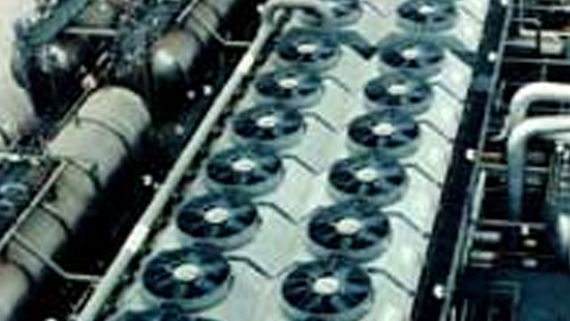
Advantages
- High velocity
- Reduces hot air recirculation
- Plenums protect the exchanger bundle from the elements
- Better air distribution across the bundle
- Better process control and stability due to plenum covering 60% of the bundle area
Disadvantages and limitations
- Possibly higher horsepower requirements if the effluent air is very hot.
- Effluent air temperature should be limited to 220F to prevent damage to fan blades, bearings, or other mechanical equipment in the hot air stream. When the process inlet temperature exceeds 350F, forced draft design should be considered because high effluent air temperatures may occur during fan-off or low air flow operation.
- Fans are less accessible for maintenance, and maintenance may have to be done in the hot air generated by natural convection.
- Plenums must be removed to replace bundles
Forced Draft Configuration
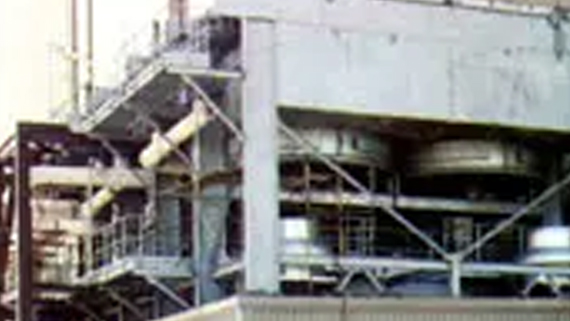
Advantages
- Lower horsepower requirements
- Maintenance personnel protected from high exit air temperatures
- Well suited for high temperature service
Disadvantages and limitations
- Less uniform distribution of air over the bundle.
- Increased possibility of hot air recirculation, resulting from low discharge velocity from the bundles, high intake velocity to the fan ring, and no stack.
- Low natural draft capability on fan failure.
- Low natural draft capability on fan failure.
- Complete exposure of the finned tubes to sun, rain, and hail, which results in poor process control and stability.
In most cases the advantages of induced draft design outweigh the disadvantages.